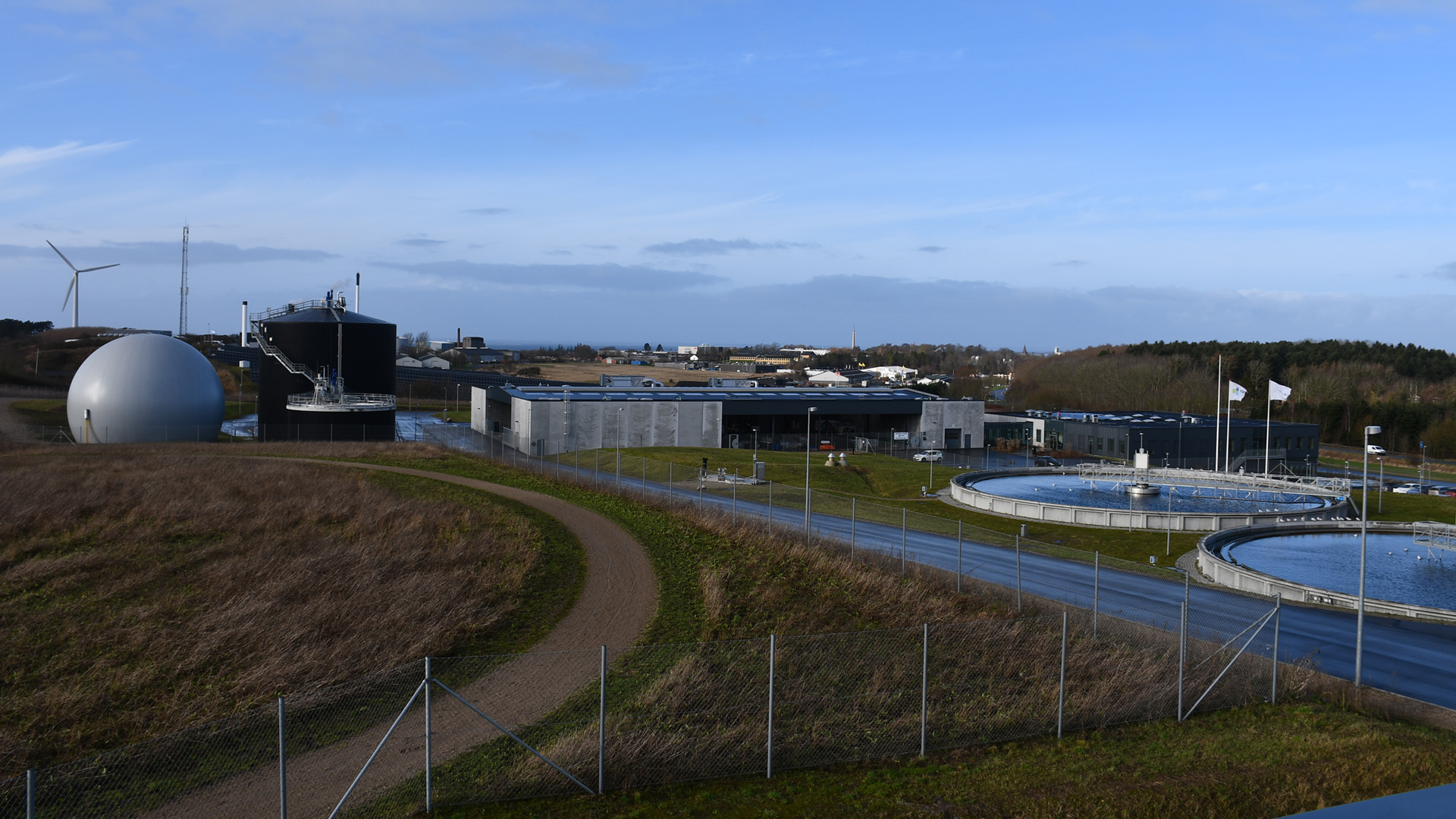
The Danish utility Assens Forsyning has established a brand new wastewater treatment plant that centralises eight existing plants, with a focus on reliability and efficiency integrated into all phases. The ambition is to be at the forefront of both technology and environmental requirements.
When discussing future water supply and wastewater treatment, the focus is often on efficient operation, flexibility and green transition. This is also the case in Assens where they have built a new wastewater treatment plant from scratch – designed to handle future requirements in terms of capacity, environmental considerations and digital technology.
Centralisation for 42,000 consumers
The new wastewater treatment plant will consolidate treatment from eight previous plants and serve the entire supply area, which has approximately 42,000 consumers. The merger requires new piping, but in many places, the old piping was already worn out and in need of renovation. In addition, several plants and pipes were undersized. So, something had to be done.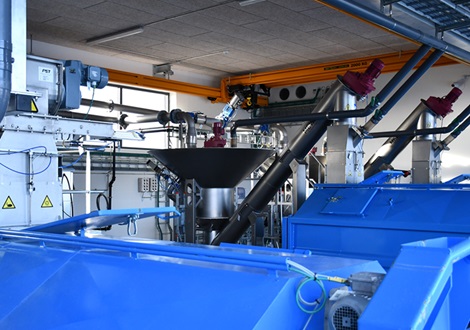
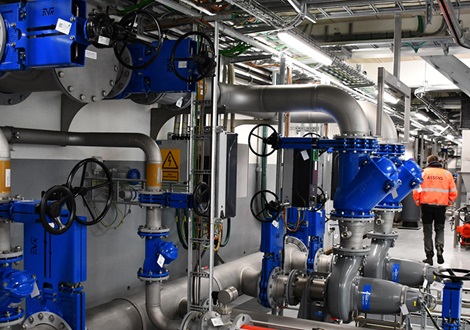
Flexible and future-proof dimensioning of the treatment plant
The centralisation allows for significant operational optimisations and ensures compliance with the revised 2025 EU Urban Wastewater Treatment Directive – including the requirement for energy-neutral operation and removal of environmentally hazardous substances from the wastewater, for all plants with a capacity above 10,000 PE. In addition, rainwater and wastewater can be kept separate with the new pipe system, so that rainwater is not pumped and treated as wastewater, which saves resources.It is a major, long-term project. The new plant is dimensioned to handle up to 1,080 m³ of wastewater per hour, but once all eight previous plants have been disconnected and all wastewater is directed to the new plant, the volume is expected to be approximately 600 m³ per hour. This flexibility is an important part of the approach focusing on future-proof operation and reliability.
Reliability at every stage
Centralisation of wastewater treatment means increased requirements for operational reliability. Therefore, the new plant is built with redundancy in all critical components: tanks, pipes, pumps and electrical installations. This ensures continuous operation and reduces the risk of nuisance in the event of breakdowns or during maintenance.Sensors and a system to control, regulate and monitor pumps ensure continuous insight into processes at the plant and enable remote monitoring and real-time optimisation.
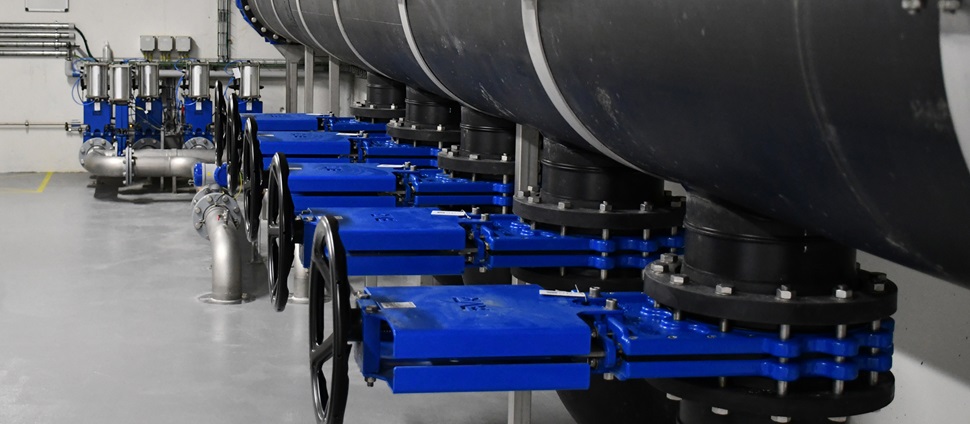
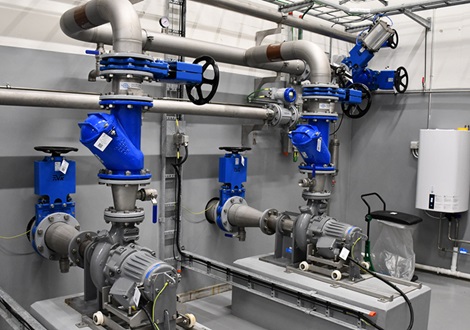
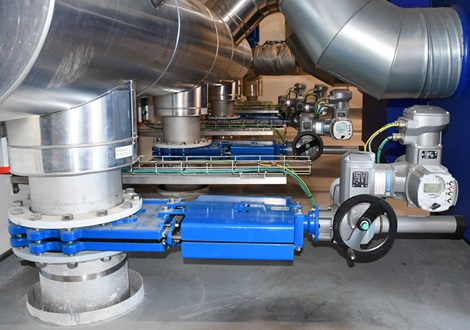
Energy-neutral operation and optimised purification process
The treatment plant is built using gravity from the inlet through the treatment tanks. This significantly minimises energy consumption, as the wastewater only needs to be actively pumped in a few places, such as when transporting return sludge.Precise and energy-efficient control of oxygen for aeration
To further optimise energy consumption, the oxygen supply for aeration in the tanks is regulated by sensor-controlled turbo blowers. Fans in four different sizes have been installed, and the most energy-efficient fan for the current need is automatically selected. This is further complemented by a knife gate valve with an actuator on each turbo blower, which regulates the air volume from the fan with high precision.Extraction of energy from wastewater
The complete treatment plant also includes an integrated biogas plant with a digester, buffer tank and biogas balloon. Here, energy is extracted from the wastewater. Some of the energy is used at the plant, and surplus energy is sent to the heat network as district heating. The new plant follows the climate ambitions of the local municipality and must be energy-neutral no later than 2050. However, by 2024, the plant was already 60% self-sufficient in terms of electricity and heating.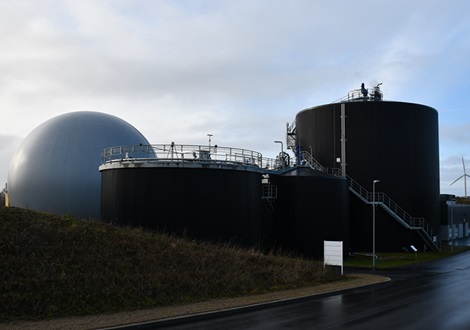
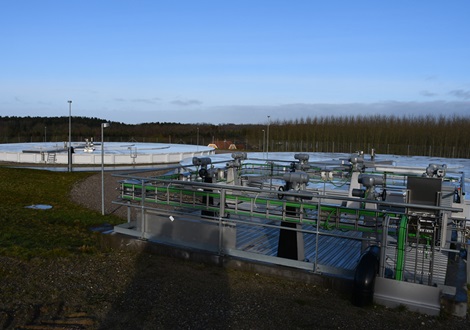
Biological purification in serial process tanks
Not only energy consumption has been optimised at the modern plant – so has the treatment process in the tanks. The biological treatment steps are optimised using a step-feed system with three serial process tanks, as opposed to traditional parallel-connected tanks. Technology distributes the wastewater to the three tanks according to capacity. Some of the wastewater flows through one tank, some through two and some through all three. Each stage (tank) has the same effect as a treatment stage in a plant with parallel-connected tanks. This means that the wastewater is often treated more thoroughly using the step-feed system. And it results in much lower values in the treated water discharged from the plant.Working environment and community involvement
The working environment is a high priority at the new plant as well. All pumps are mounted on rails for easy access during maintenance and repairs, and most of the plant is equipped with crane coverage. Additionally, there is plenty of space around most installations.It is important for the utility to involve the local community. Therefore, the plant buildings feature large windows, communication boards around the plant area and a publicly accessible roof terrace on one of the buildings, from where there is a view of both the biogas plant and the biological treatment tanks. Combined with a school service and laboratory facilities in the administration building, this is an important step toward increasing awareness of our shared water resources.
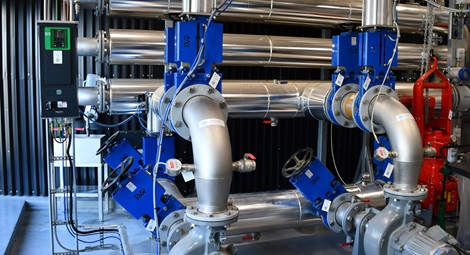
AVK valves delivered to the project
- Knife gate valves with LINAK linear actuator, double-acting pneumatic actuator or handwheel, 152 pcs. DN65-350
- Ball check valves, 30+ pcs. DN80-250
- Gate valve, 1 pcs. DN700
- Butterfly valves
The valves were supplied by Vatech 2000, who also supplied dampers with AUMA actuator Ø500-800 for the project.

AVK knife gate valves
Knife gate valves are designed mainly for on-off and isolation services in systems with high content of suspended solids. They can withstand even the harshest environments and are particularly advantageous for handling sludge as well as viscous, corrosive and abrasive media.
We offer knife gate valves with lever, handwheel, pneumatic actuator, ISO top flange for actuator or complete with electric or pneumatic actuator.
AVK range of knife gate valves